
Continuous Improvement Through Manufacturing Automation
A critical component to the angioplasty syringe was the bourdon tube pressure gauge, of which was assembled with nine manual operations. The first four, especially when inserting the bourdon tube tip to movement link arm was the most important operation that affected calibration. The line had suffered more than ten percent returns from customers amounting to a large amount of rework. After much investigation, I lead a team to design and build a semiautomated turntable assembly machine. The machine fixtured the components, sensed the geometry after each assembly step, and maintained normality of the tip attachment. The line was able to reduce staff, go from two shifts to one shift, and reduce returns to less than one-percent.
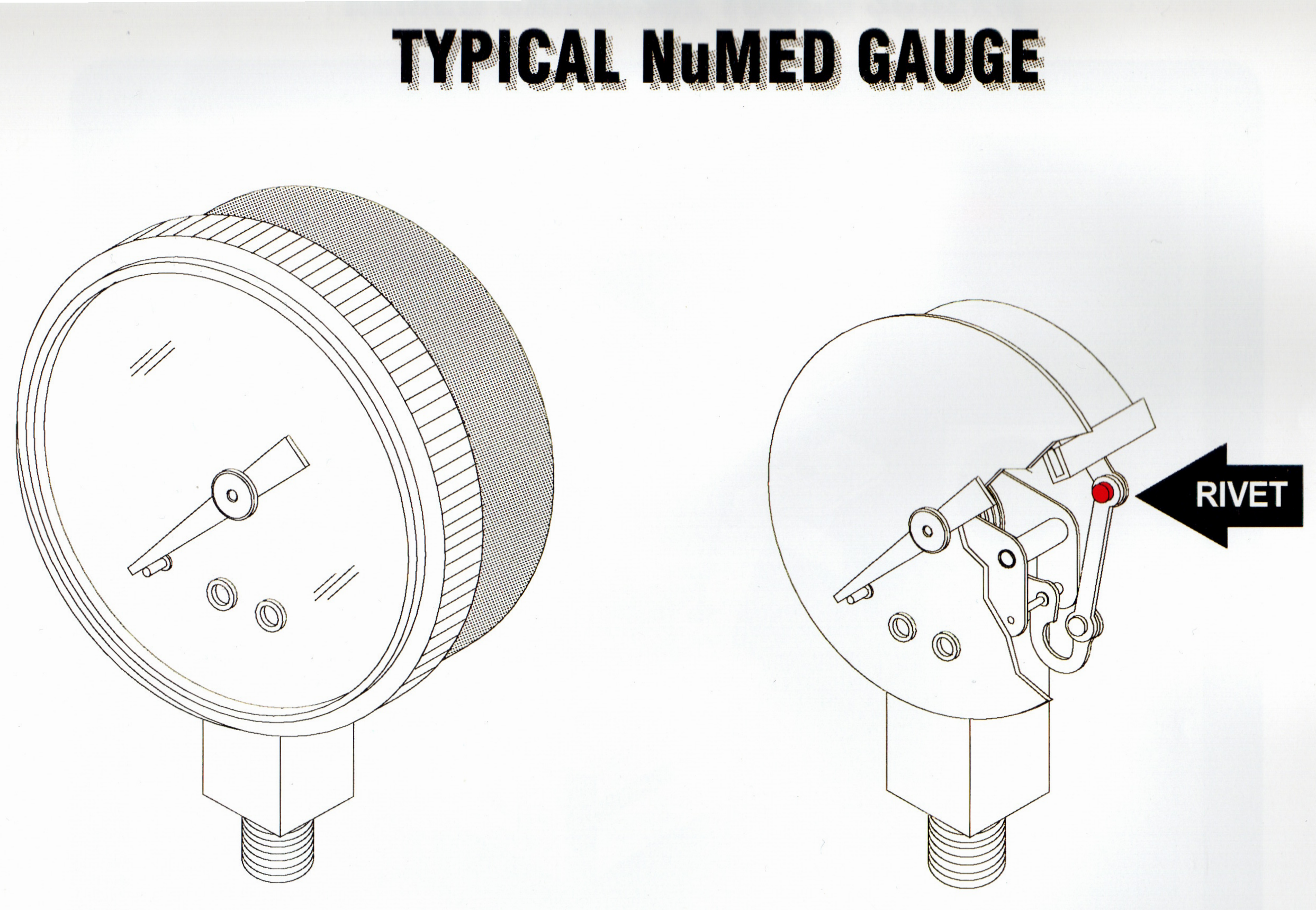


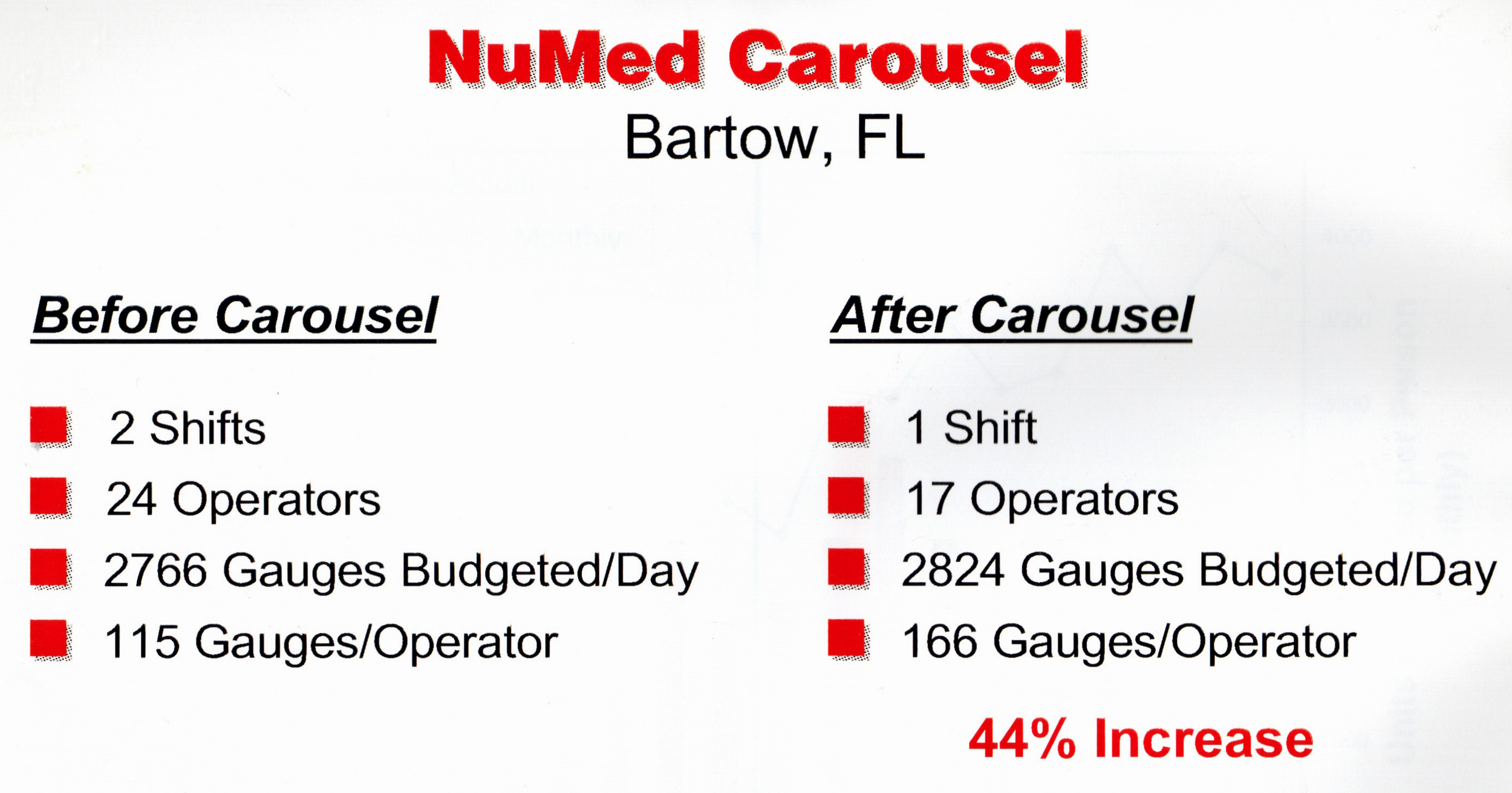
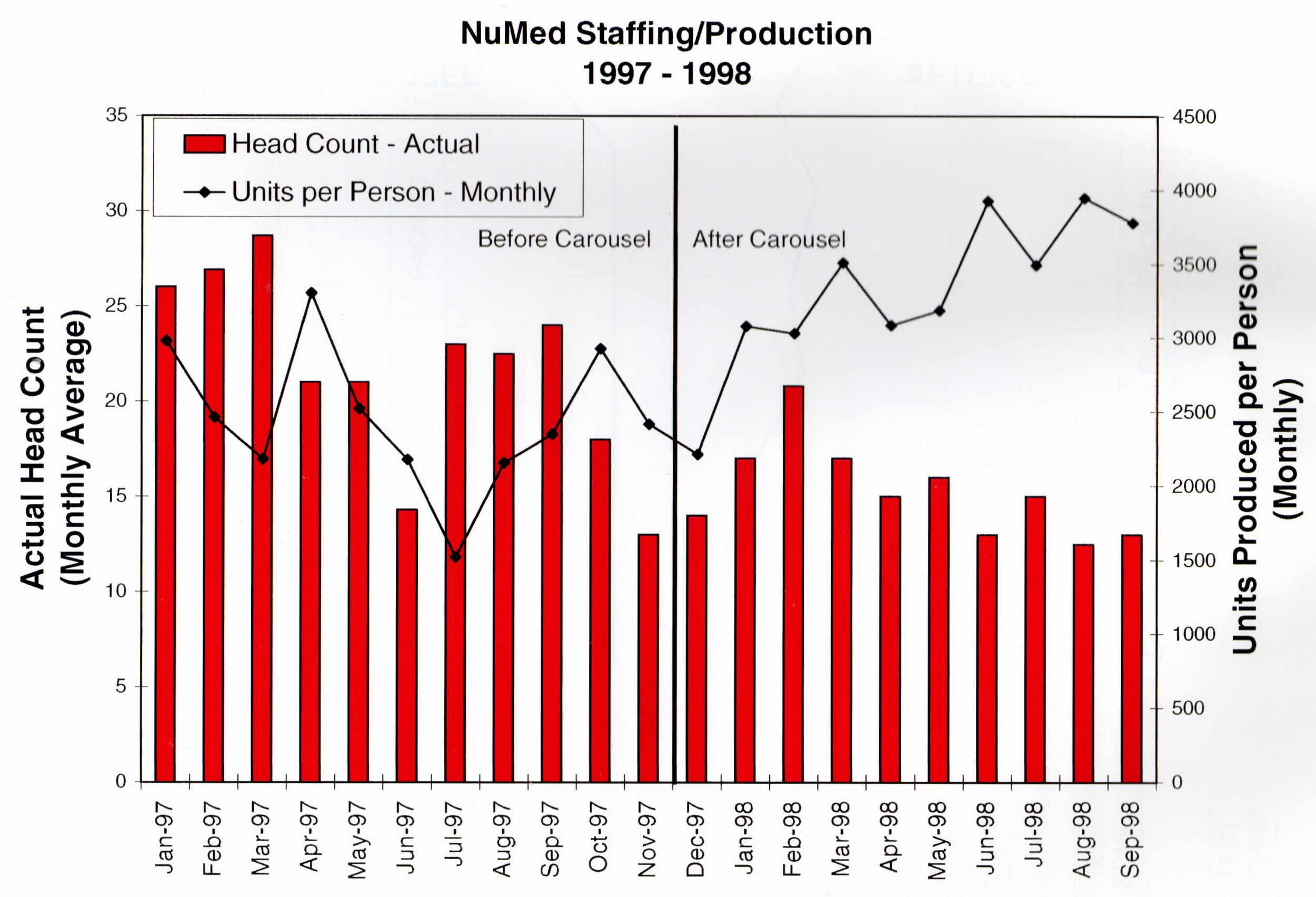
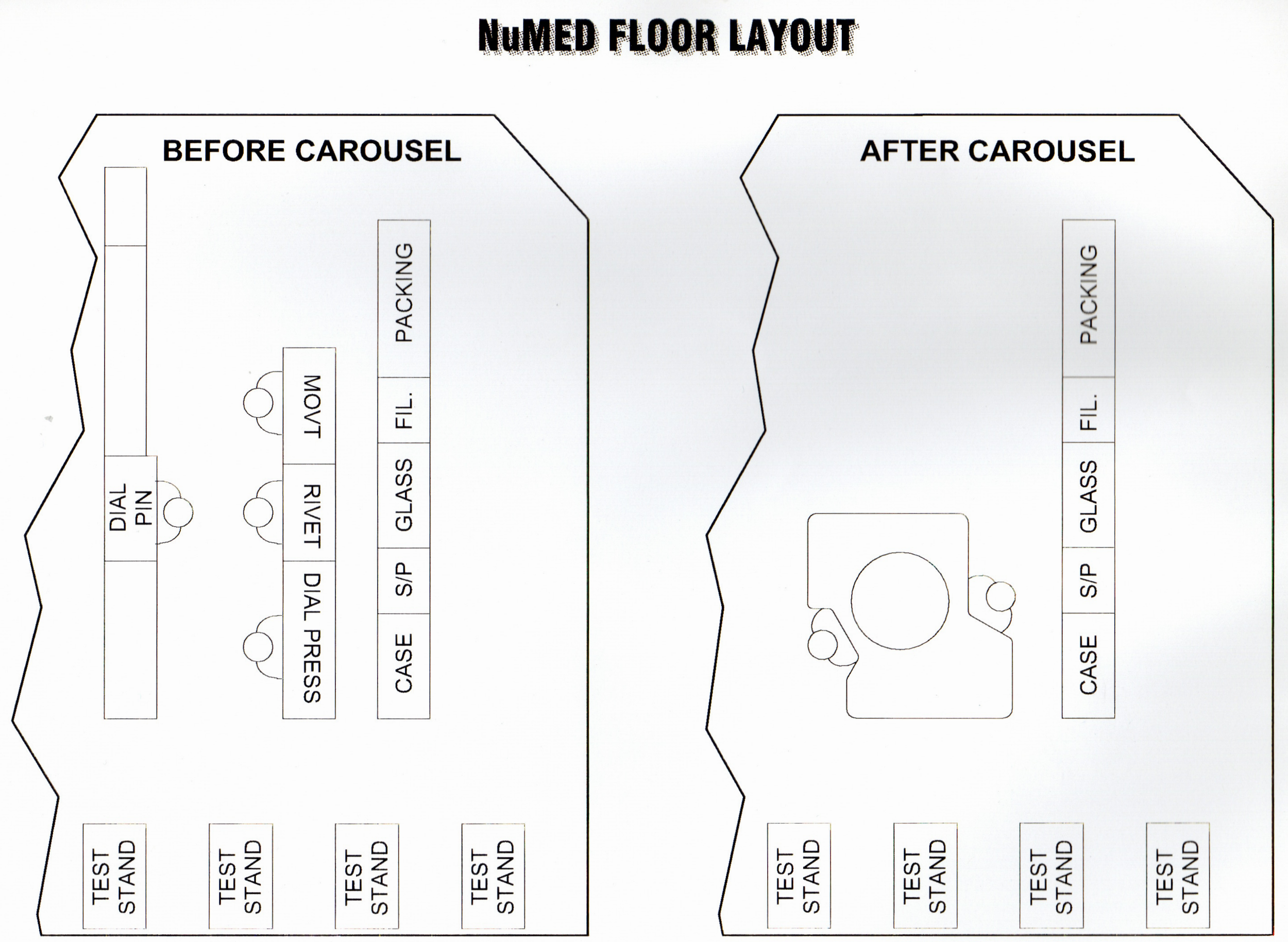
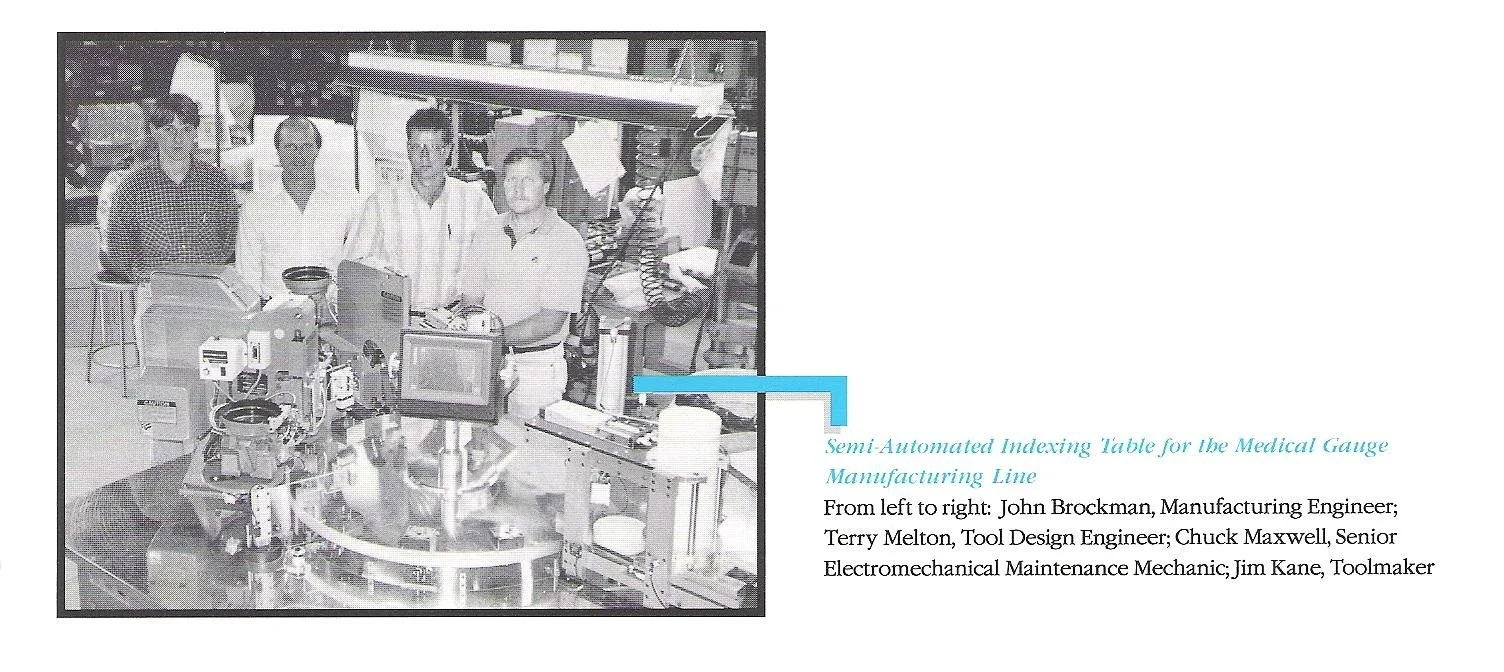